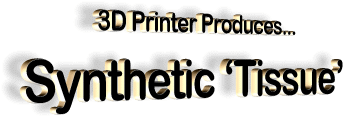
April 05, 2013
from
RT
Website
Spanish version
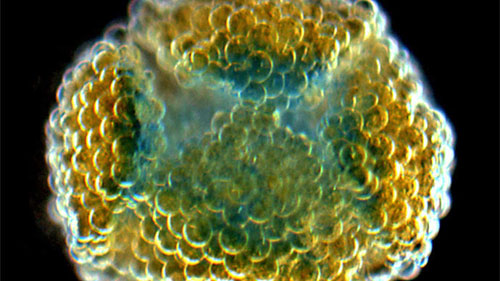
Droplet
network that self-folded
into hollow ball
c.400 microns across
(credit: Oxford
University / G Villar)
Researches have built a new type of 3D printer that creates
tissue-like material that could revolutionize medicine.
The artificial material produces the
properties of living tissues and could potentially replace them in
the future. The new material developed by scientists at Oxford
University consists of water, coated and protected by lipid
molecules.
The tens of thousands of 3D connected
caviar-like droplets were named 'droplet networks'.
“We add chemicals and bio chemicals.
This changes the water. After all we humans are made of networks
of water droplets” Professor Hagan Bayley of Oxford University's
Department of Chemistry commented, as cited by the Daily Mail.
The 'droplet networks' could one day
replace damaged living tissue or deliver drugs to specific
locations, the researchers said in a study released Friday in
Science magazine.
"We aren't trying to make materials
that faithfully resemble tissues but rather structures that can
carry out the functions of tissues," said Professor Bayley in a
news briefing on the Oxford university website.
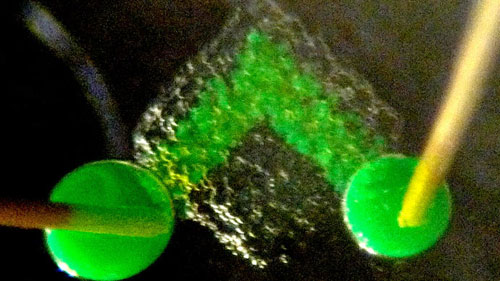
Droplet network c.500
microns across
with electrically
conductive pathway
between electrodes
mimicking nerve
(credit: Oxford
University / G Villar)
"The droplets can be printed with
protein pores to form pathways through the network that mimic
nerves and are able to transmit electrical signals from one side
of a network to the other," he added.
Eventually this material could replace
the use of stem cells, a completely synthetic material, has no
genome and does not replicate. The creation of 'droplet networks'
avoids many problems such as harvesting living tissue.
The Oxford scientists said that there was no printer to build these
aqueous droplets as so far they have developed 3D printers that can
only create solid objects. So they found a way out by building one
in their laboratory.
The unique 3D printer was built by
Gabriel Villar, a student and the lead author of the paper.
"Conventional 3D printers aren't up
to the job of creating these droplet networks, so we custom
built one in our Oxford lab to do it," said Professor Bayley.
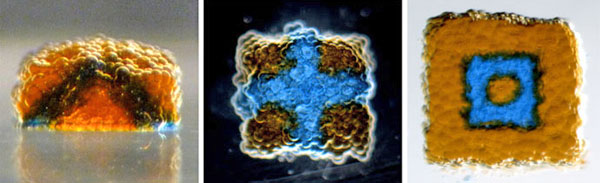
Printed droplet
networks c.500 microns across
(Credit: Oxford
University / A Graham)
Each droplet is 50 microns in diameter, about 0.05 millimeters, but
it is five times larger than a living cell.
Professor Hagan Bayley said that
given more time and funding they will be able to develop smaller
networks.
"At the moment we've created
networks of up to 35,000 droplets but the size of network we can
make is really only limited by time and money. For our
experiments we used two different types of droplet, but there's
no reason why you couldn't use 50 or more different kinds."
At present the material remains stable
for weeks.
This synthetic material can be designed to take on different shapes
after it was printed. This resembles muscle movement. The
researchers have demonstrated the through the creation of a
flowerlike droplet network that from the initial flat shape curls
into a sphere.
The movement is triggered by a process called osmosis.
The droplets on the bottom of the network are filled with a high
concentrated solution, and the ones on the top are filled with a low
concentration. After the droplets are printed the solvent molecules
on top flow into the droplets on the bottom through a partially
permeable membrane.
When that happens the droplets on top
shrink and the droplets on the bottom blow up causing the whole
structure to curl.
3D printing gives vast opportunities such as to create objects as
complex as human organs.
There are certain advantages of using
artificial tissue in comparison with living tissue, says Cameron
Ferris a research associate from the ARC Centre of Excellence
for Electromaterials Science at the University of Wollongong,
ABC Science reports.
He is part of a team that develops 3D
printers to potentially create replacement organs using living
cells.
"It's incredibly expensive to
harvest stem cells [for 3D printing of living tissue], and the
food you have to feed them, to grow and expand them so that you
have enough stem cells to print takes some time” he said,
according to ABC science.
Hear, hear!...
Scientists Create Human-Like Ears
...with 3D
Printing
February 21, 2013
from
RT
Website
Spanish version
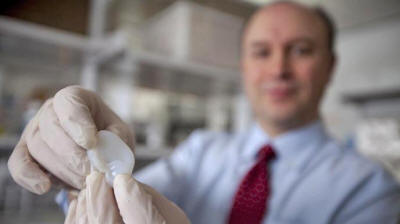
Larry Bonassar,
Cornell Associate
Professor of Mechanical Engineering.
(AFP Photo / Lyndsay
France)
The latest innovation in 3D printing -
artificial ears - feel, look and behave identically to human ones.
The new product developed in the US could provide patients who are
missing all or just part of their ear with a chance at
reconstructive surgery.
Cornell biomedical engineers and Weill Cornell Medical College
physicians published their study online in the PLOS ONE journal on
Wednesday.
They show how they developed an ear over the course of three months
by inserting living cells into an injection mold and then growing
cartilage in the shape of its mold.
"This is such a win-win for both
medicine and basic science, demonstrating what we can achieve
when we work together," co-lead author Lawrence Bonassar,
associate professor of biomedical engineering at Cornell, told
AP.
According to the study, the first
implant could be tried in around three years.
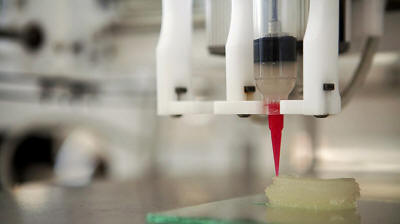
A 3-D printer.
(AFP Photo / Lyndsey
France)
Researchers began the project by creating a digitized 3D image of a
human ear, which was used to build an ear-shaped mold using a 3D
printer.
Then they injected a gel made of living cow ear cells and collagen
(a substance used to make gelatin) into the mold and the ear was
done.
The production part took less than two days: only half a day to
build the mold, a day to print it, 30 minutes to insert the gel,
then wait 15 minutes and everything was ready to go.
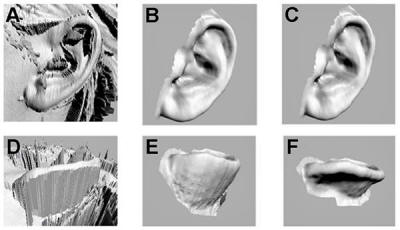
Digitization process for human ears.
(Image from
plosone.org)
Scientists tested the artificial ears by implanting them on the
backs of rats and it took one to three months for the ears to grow.
Rodents are often used by scientists to test the growing of
artificial ears.
"We trim the ear and then let it
culture for several days in nourishing cell culture media before
it is implanted," Bonassar told AP.
The need for the product is there.
Thousands of children who are born with ear deformities and those
who have lost an ear during their life could benefit from the new
technology.
The most common deformity is microtia, when the external ear does
not fully develop. In US one to four children per 10,000 are born
with it, according to the study.
People born with microtia usually have an inner part of the ear
fully functional, but they still have impaired hearing because they
are missing part of their external ear.
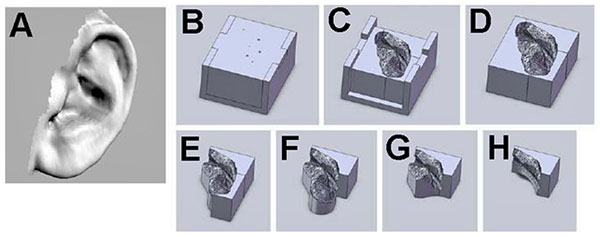
Mold design
based on ear anatomy.
(Image from
plosone.org) )
"A bioengineered ear replacement
like this would also help individuals who have lost part or all
of their external ear in an accident or from cancer," co-lead
author Jason Spector told Live Science.
Researchers identified the best time for
implantation for the kids to be at around the age of five or six,
when the ears are at 80 per cent of their adult size.
The study says that a chance of rejection during implant procedure
could be potentially decreased by using human cells from the same
patient when constructing the bioengineered ear.
Before this point, technology only allowed to build replacement ears
with a foam-like consistency or by using a patient's harvest rib,
the latter is a painful process and ears still often looked
unnatural and did not properly work.
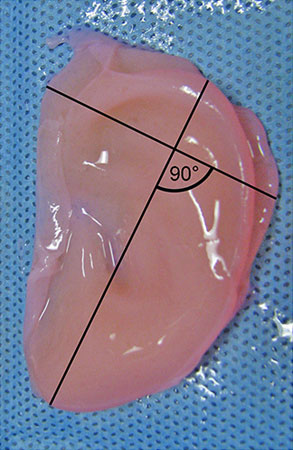
Schematic
representation of length and width measurements.
(Image from
plosone.org)
A Tissue-Like Printed Material
April 2013
from
2n2n
Website
Spanish version
British researchers said in
a report published in the journal
"Science", they use a special 3D printer to print out material
similar to the biological tissue, this outcome expected future
applications in the medical field.
This report is published jointly by Professor Hagan Bayley of
the University of Oxford and colleagues.
According to reports, they take
advantage of the the 3D printer hierarchical profuse droplets of
lipid film wrapped, these droplets form a mesh structure, constitute
a special new material.
The researchers say, to print out the material texture with brain
and adipose tissue similar folding action can make a similar
muscle-like activities, with work like neurons as the communication
network structure can be used to repair or enhance the failure of
the organ. Synthetic materials, it also avoids the problems caused
by some the way manufacturing living tissue with stem cells.
The researchers also said that conventional 3D printers can not
print this new material, experiment, they used a special 3D printer,
this printer ejected droplet diameter of approximately 50 microns, 5
living cells so but I believe will be able to reduce the size of the
droplets.
In recent years, 3D printing technology rapid development, from
engineering to aerospace, from education to health care, application
more widely.
In February of this year, Cornell
University researchers had reported that,
"They use cells from ears
of cattle on 3Dprinters to print out the artificial ear."
A Tissue-Like Printed
Material by Gabriel Villar,
Alexander D. Graham, Hagan Bayley
Science 5 April 2013: Vol. 340 no. 6128 pp. 48-52 DOI: 10.1126/science.1229495
Living cells communicate and cooperate to produce the emergent
properties of tissues.
Synthetic mimics of cells, such as
liposomes, are typically incapable of cooperation and therefore
cannot readily display sophisticated collective behavior. We
printed tens of thousands of picoliter aqueous droplets that
become joined by single lipid bilayers to form a cohesive
material with cooperating compartments.
Three-dimensional structures can be
built with heterologous droplets in software-defined
arrangements.
The droplet networks can be
functionalized with membrane proteins; for example, to allow
rapid electrical communication along a specific path. The
networks can also be programmed by osmolarity gradients to fold
into otherwise unattainable designed structures.
Printed droplet networks might be
interfaced with tissues, used as tissue engineering substrates,
or developed as mimics of living tissue.
Read the full report: "A
Tissue-Like Printed Material".
|